INDUSTRY DIGITALIZATION WITH JAHAANN
At Jahaann, we specialize in performance optimization for businesses. Our experts identify and address any drawbacks in your existing systems to optimize your processes, resulting in increased efficiency, cost reduction, and significant long-term savings. Our comprehensive system optimization services ensure that your business is running as efficiently as possible, allowing you to reach your full potential
Transform Your Plant Operations with Our Jahaann Performance Optimization Services

Energy Analysis
Get detailed energy analysis to identify inefficiencies, optimize usage and reduce costs with Jahaann’s Energy Analysis service.
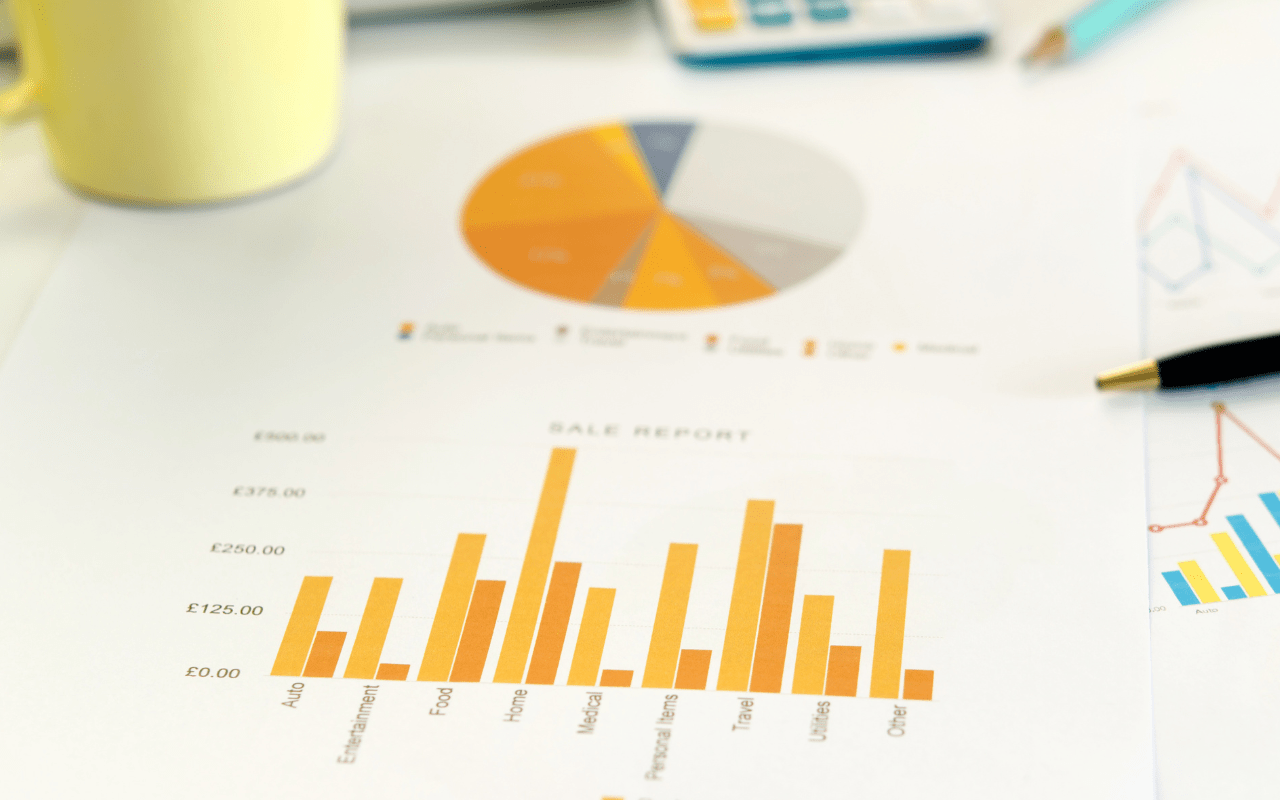
Cost Analysis
Reduce costs and maximize efficiency with Jahaann’s Cost Analysis. Identify wastage and optimize operations for maximum savings.
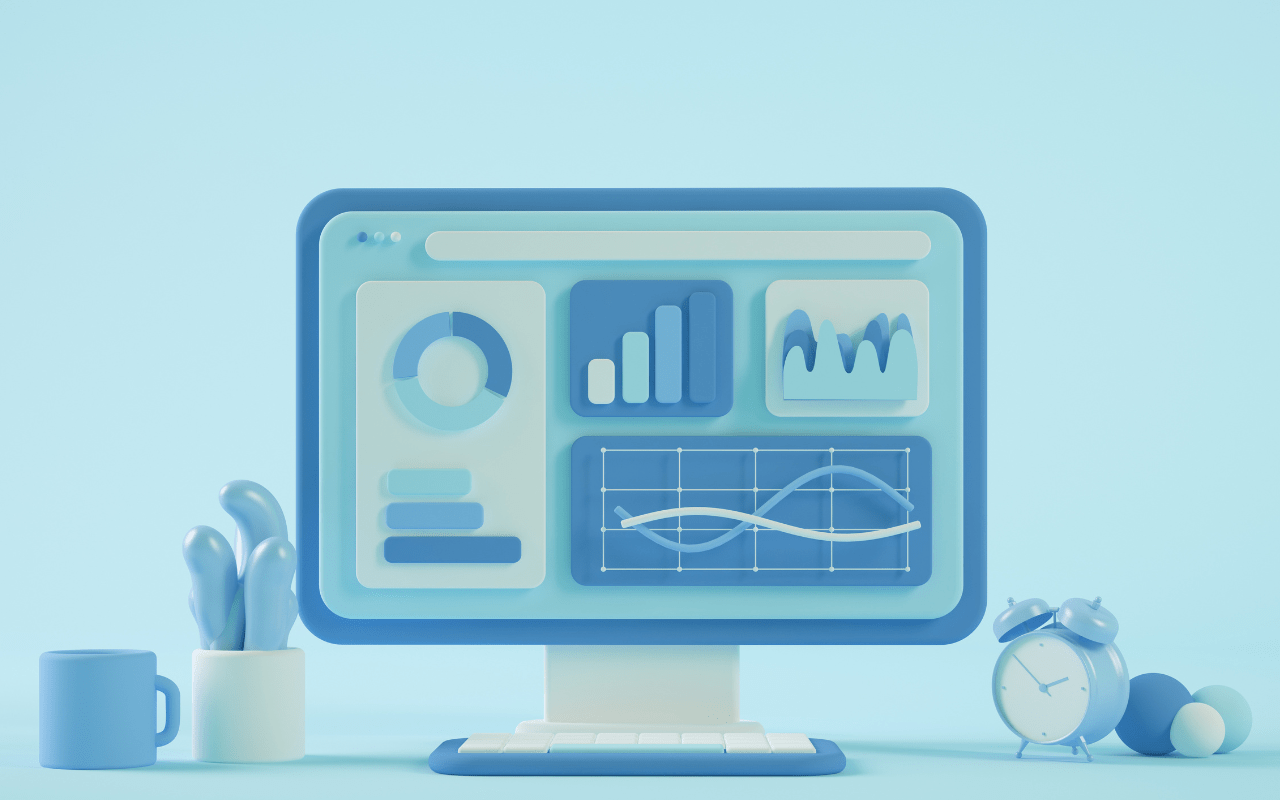
Production Analysis
Monitor gas levels, flow rates, and usage patterns to optimize consumption, reduce wastage and improve efficiency.
Frequently Asked Questions
FAQs about Jahaann
What is performance optimization?
Performance optimization is the process of identifying and implementing improvements to increase efficiency, effectiveness, and sustainability within a system, process, or organization. This can encompass various aspects, including production, cost, and energy use.
Why is performance optimization important?
- Increased production output: Improved efficiency can lead to higher production rates and shorter lead times.
- Reduced costs: Optimizing processes can minimize waste, energy consumption, and material use, leading to cost savings.
- Enhanced energy efficiency: Identifying and addressing energy inefficiencies can lower energy bills and environmental impact.
- Improved competitiveness: By optimizing performance, businesses can remain competitive in the market.
- Greater decision-making: Data-driven insights from production, cost, and energy analysis can inform better business decisions.
What are the key components of performance optimization with production, cost, and energy analysis?
- Production analysis: This involves examining production processes to identify bottlenecks, inefficiencies, and areas for improvement. This may involve data collection, process mapping, and capacity analysis.
- Cost analysis: This evaluates the costs associated with production, including materials, labor, equipment, and overhead. Identifying cost drivers and areas for cost reduction is crucial.
- Energy analysis: This assesses the energy consumption of processes and equipment. Identifying energy-intensive areas and implementing energy-saving measures can significantly impact energy efficiency.